TOTAL QUALITY MANAGEMENT
We provide a wide range of Services
“Be passionate about solving the problem, not proving your solution.”
~Nathan Furr
The total quality management concept is a process that goes beyond the physical and cultural aspects of an organization, to also include their operational and financial aspects. It can help managers assess how they can improve their organization.
The total quality management concept has been around since the early 1900s, but it got its name in the 1950s. TQM became popular in Japan after World War II because of its contribution to helping rebuild the country’s economy.
So how does it work? This model is based on three pillars: leadership, employee empowerment, and customer satisfaction. For example, if you are a manager at a company, your role as a leader is to make sure all employees understand that their skills are valuable, and they have a voice in the company’s decisions.
- All
- Business
- Front Line
- Leadership
- TQM
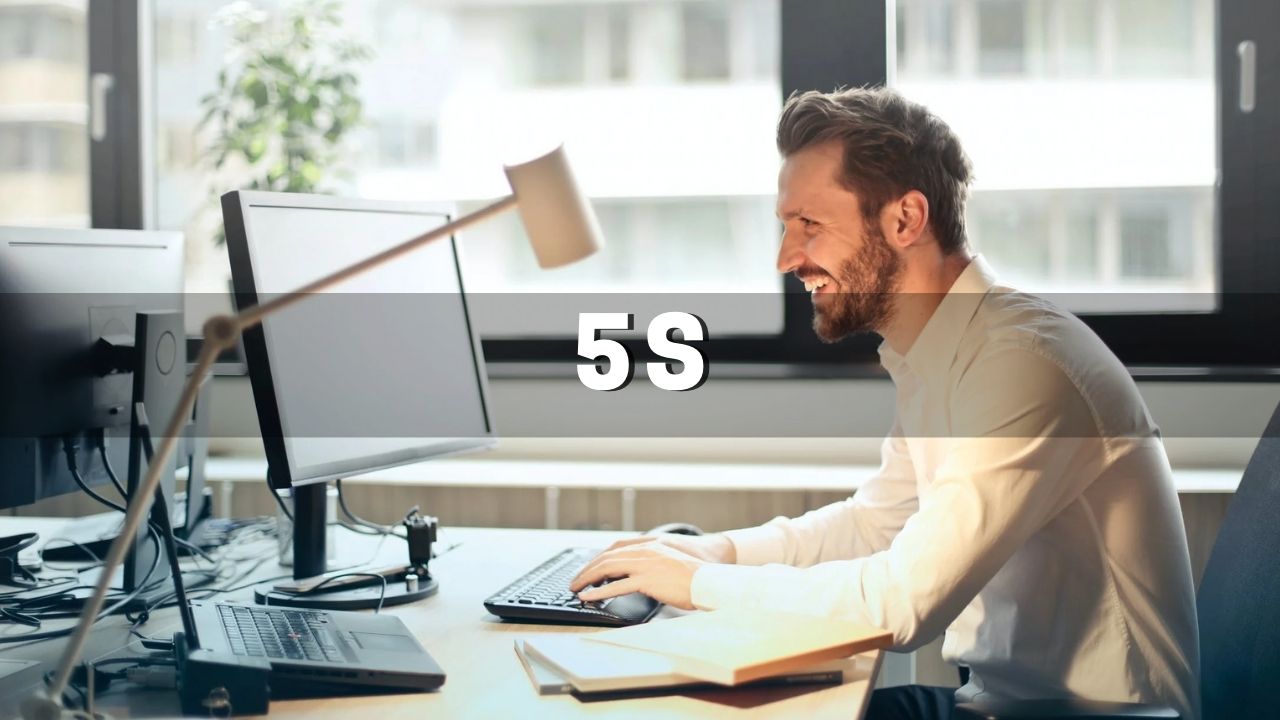
5 S
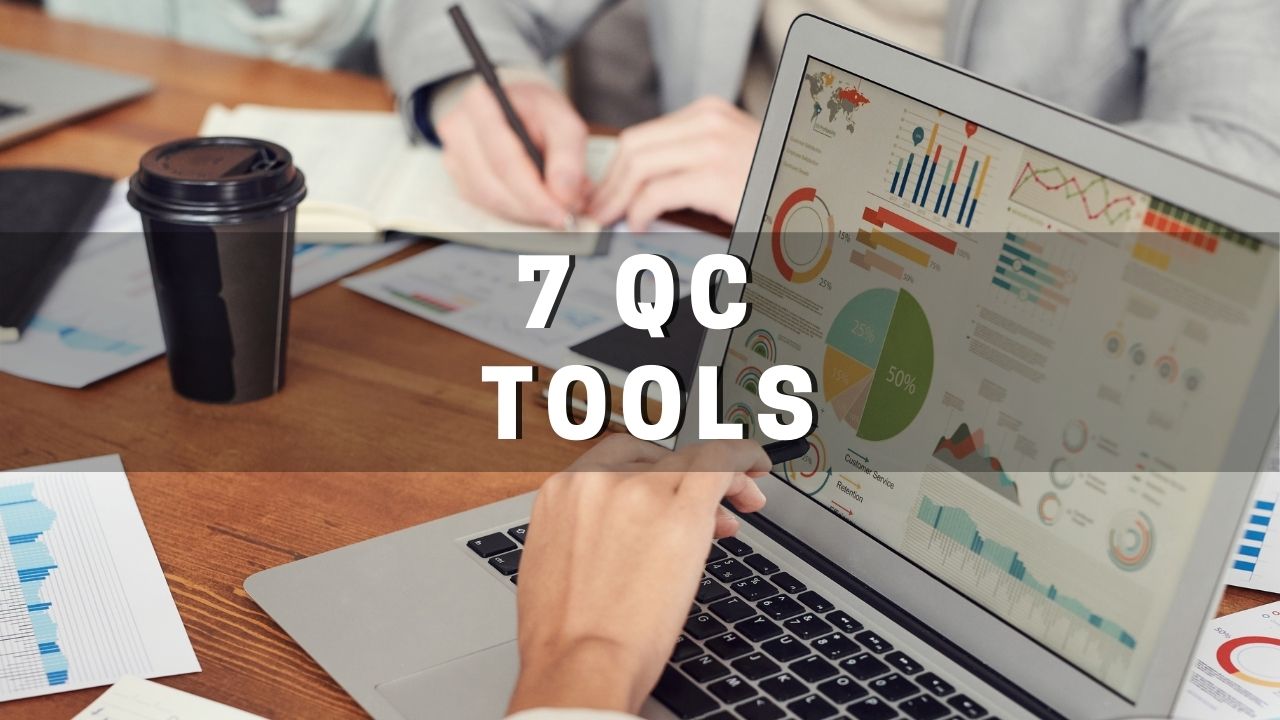
7 QC TOOLS
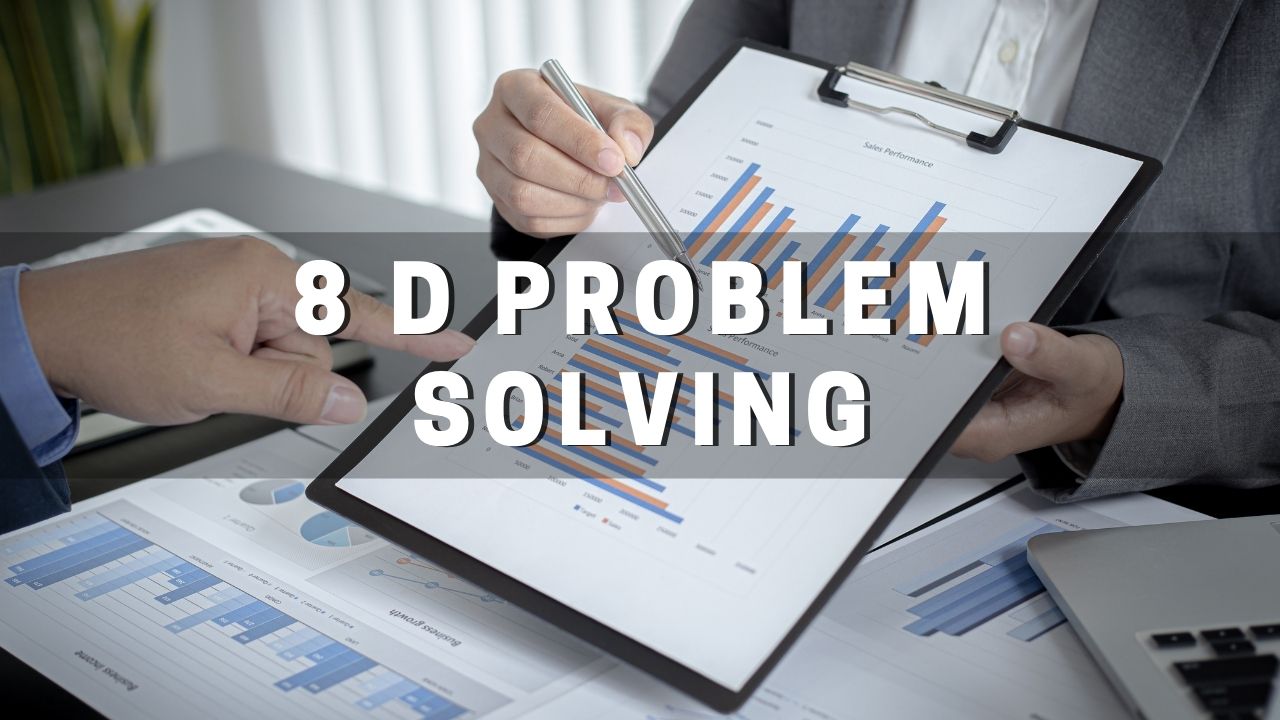
8 D Problem Solving
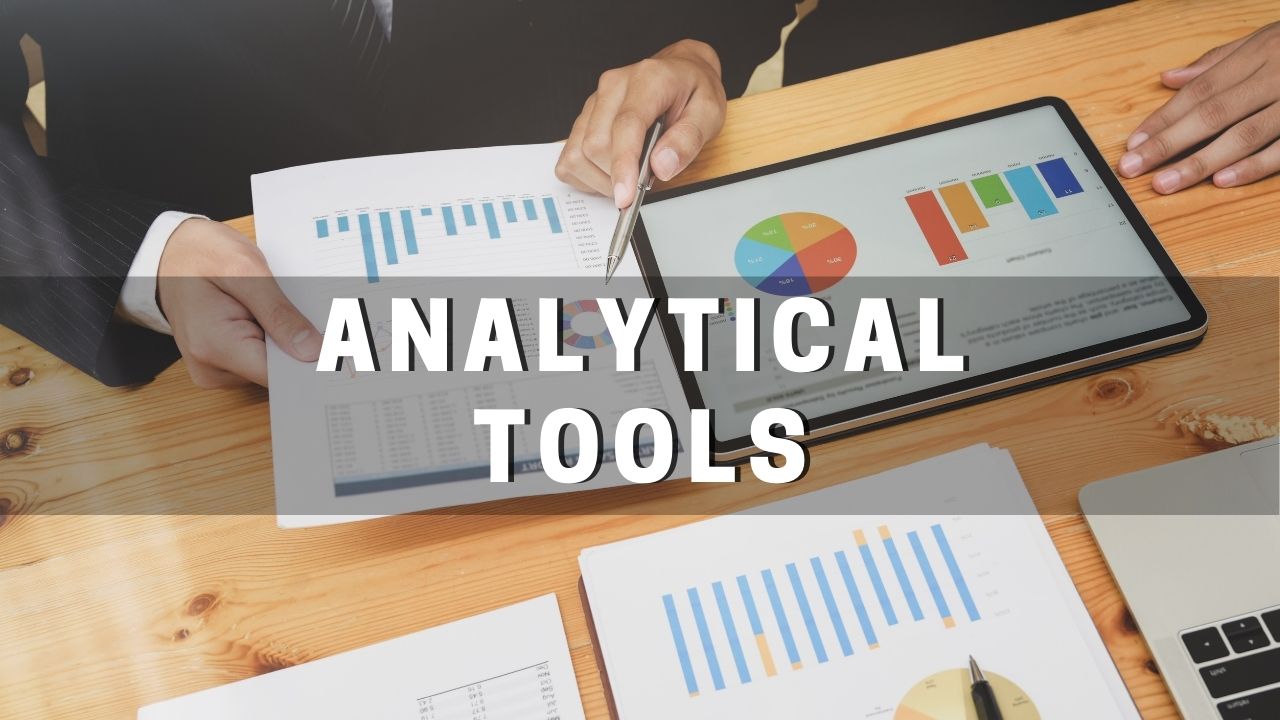
Analytical Tools and Techniques
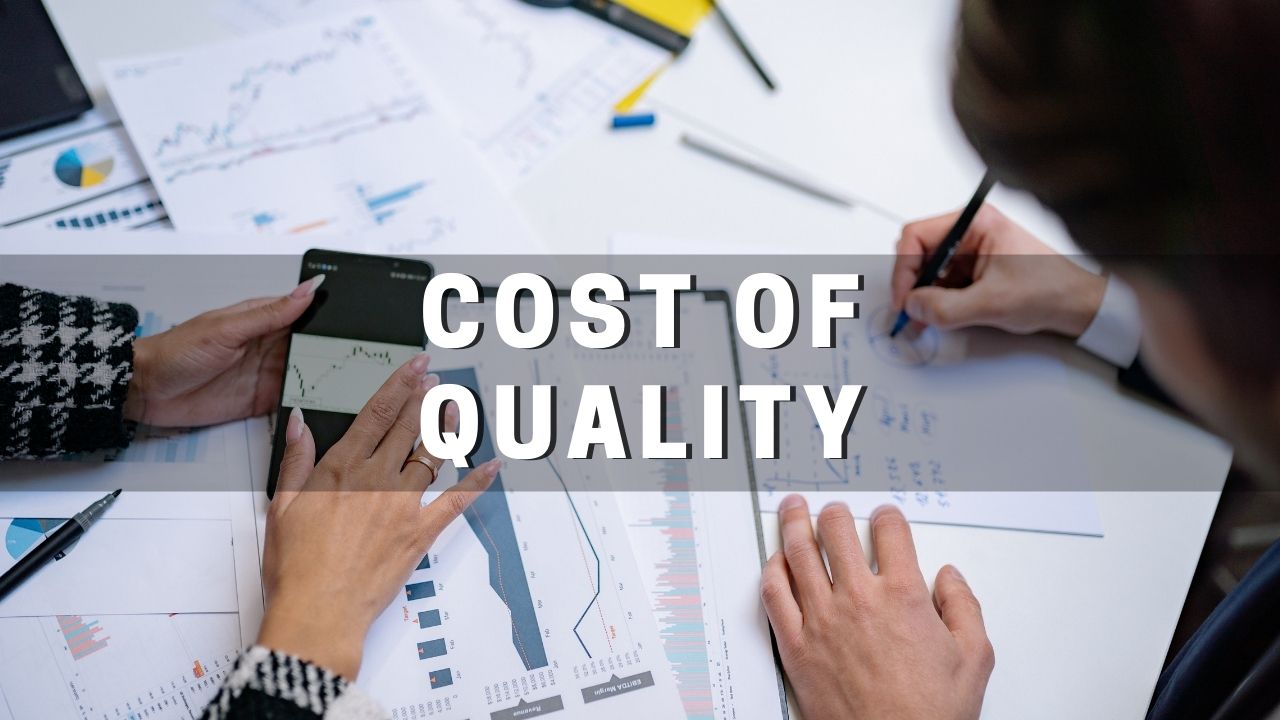
COST OF QUALITY
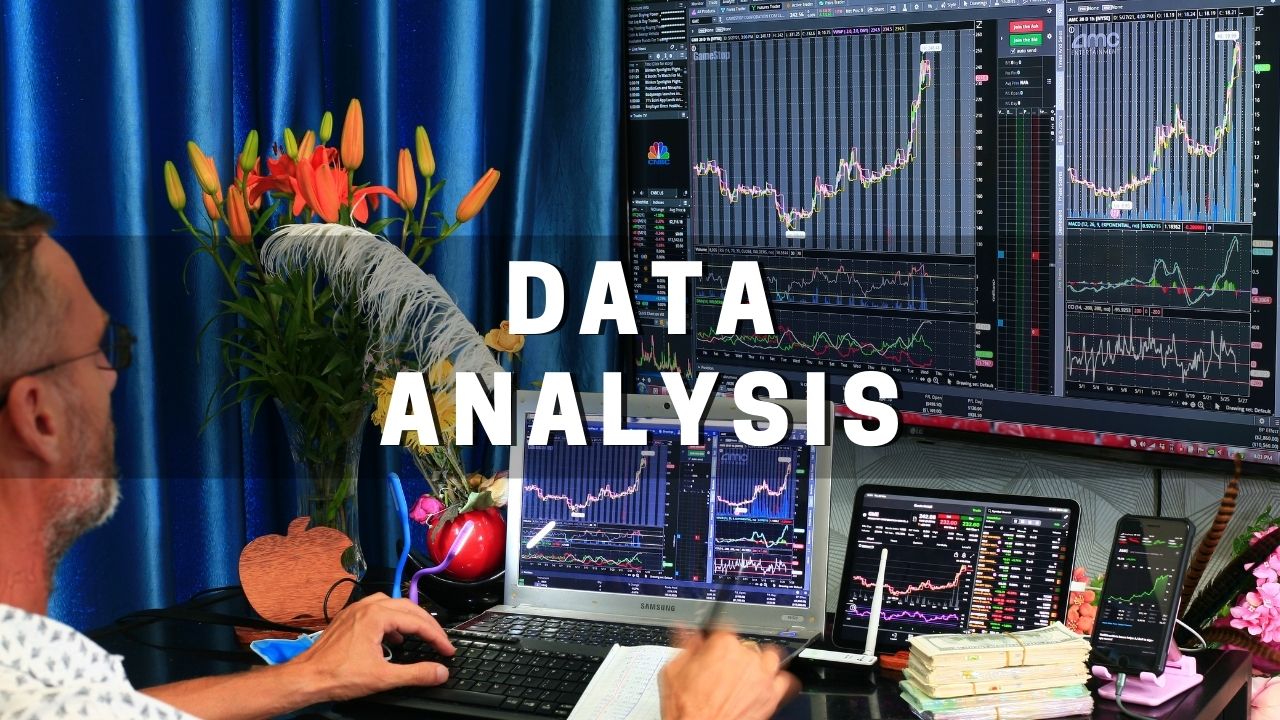
DATA ANALYSIS
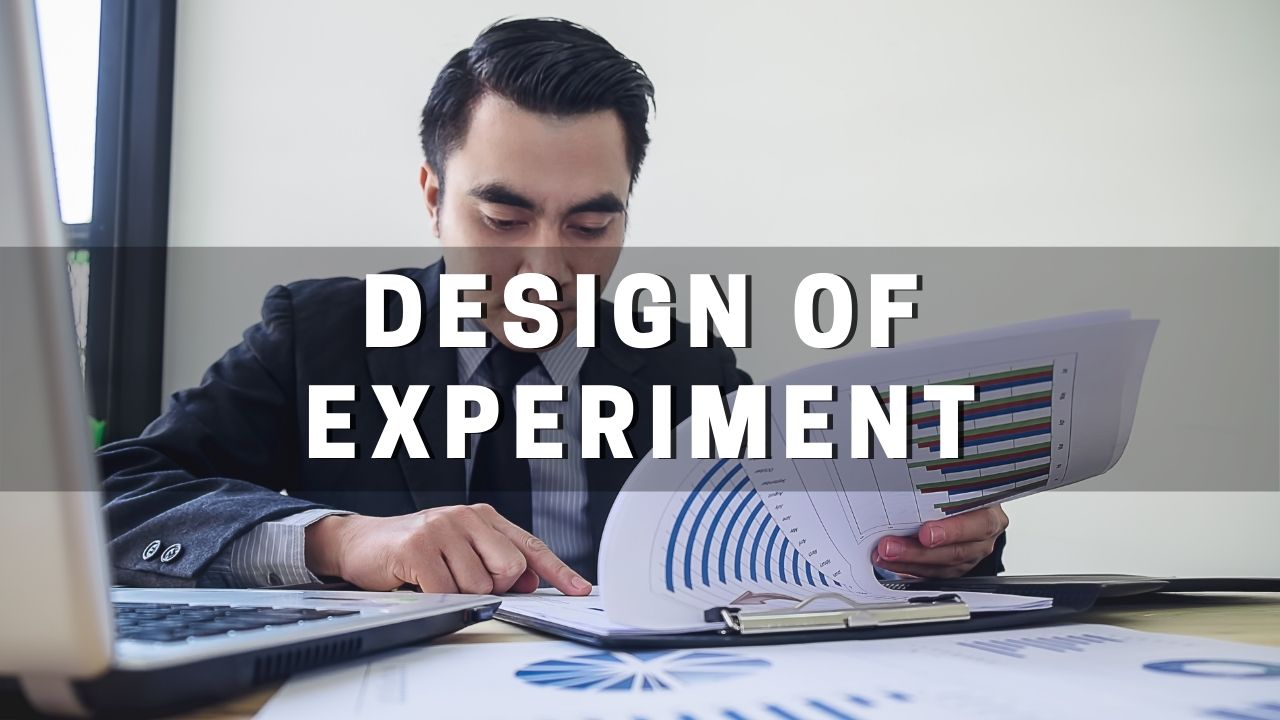
DESIGN OF EXPERIMENT
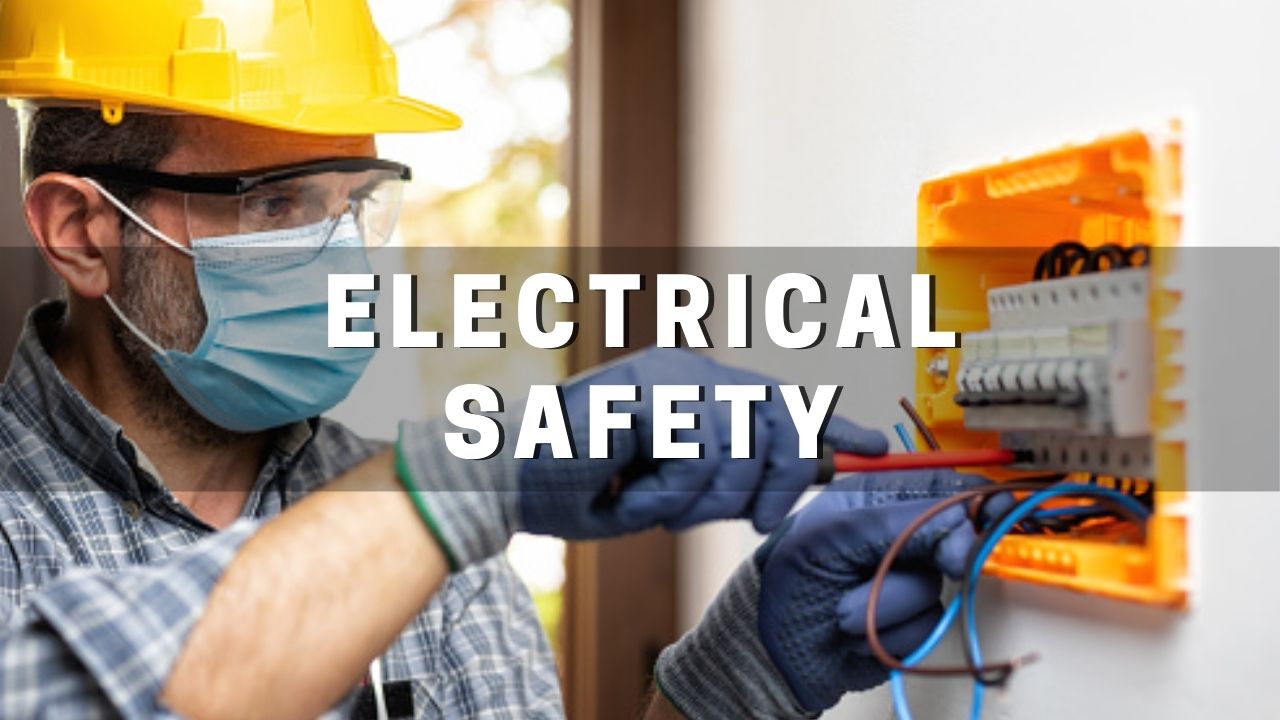
ELECTRICAL SAFETY AWARENESS
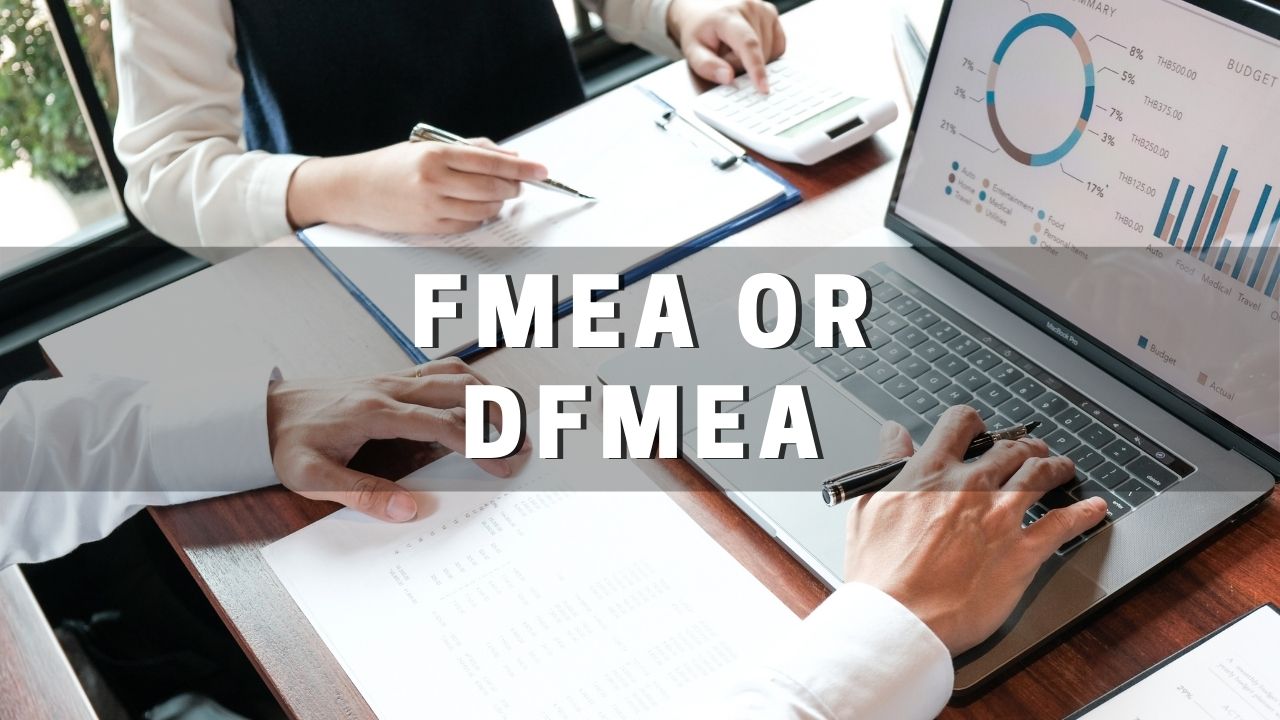
FMEA OR DFMEA – FAILURE MODE AND EFFECTS ANALYSIS
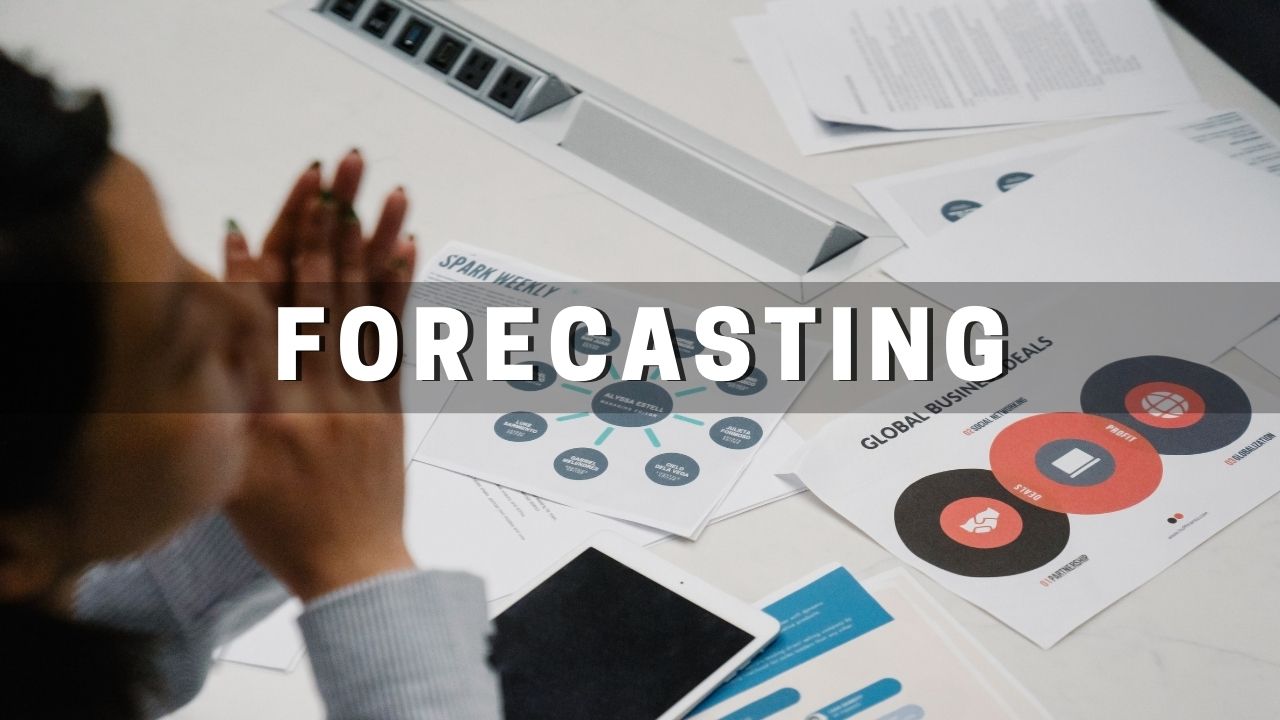
FORECASTING
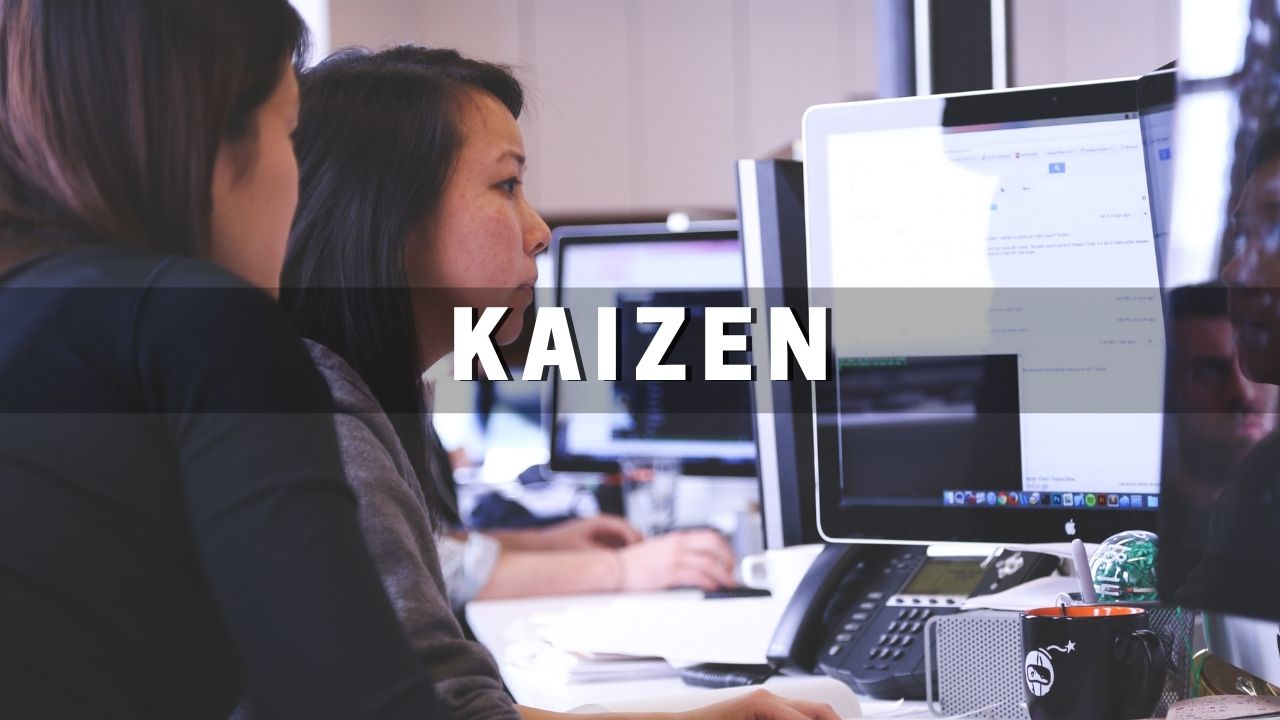
KAIZEN
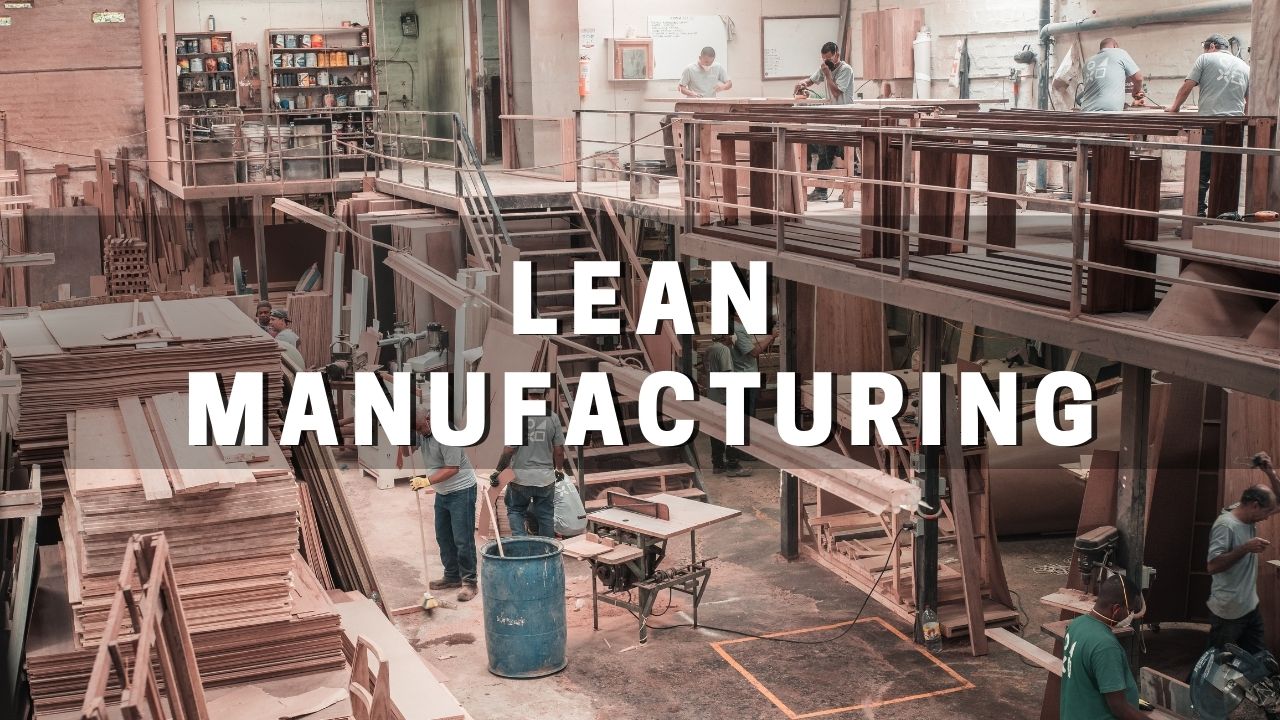
LEAN MANUFACTURING
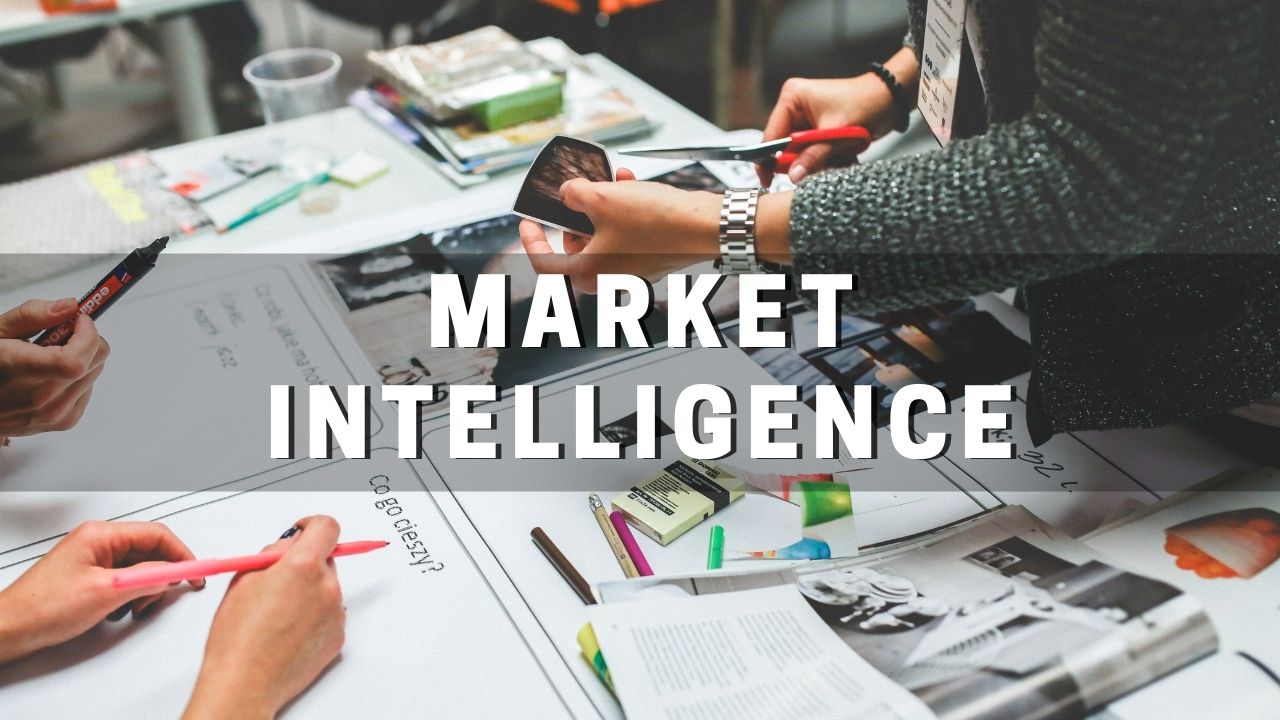
MARKET INTELLIGENCE
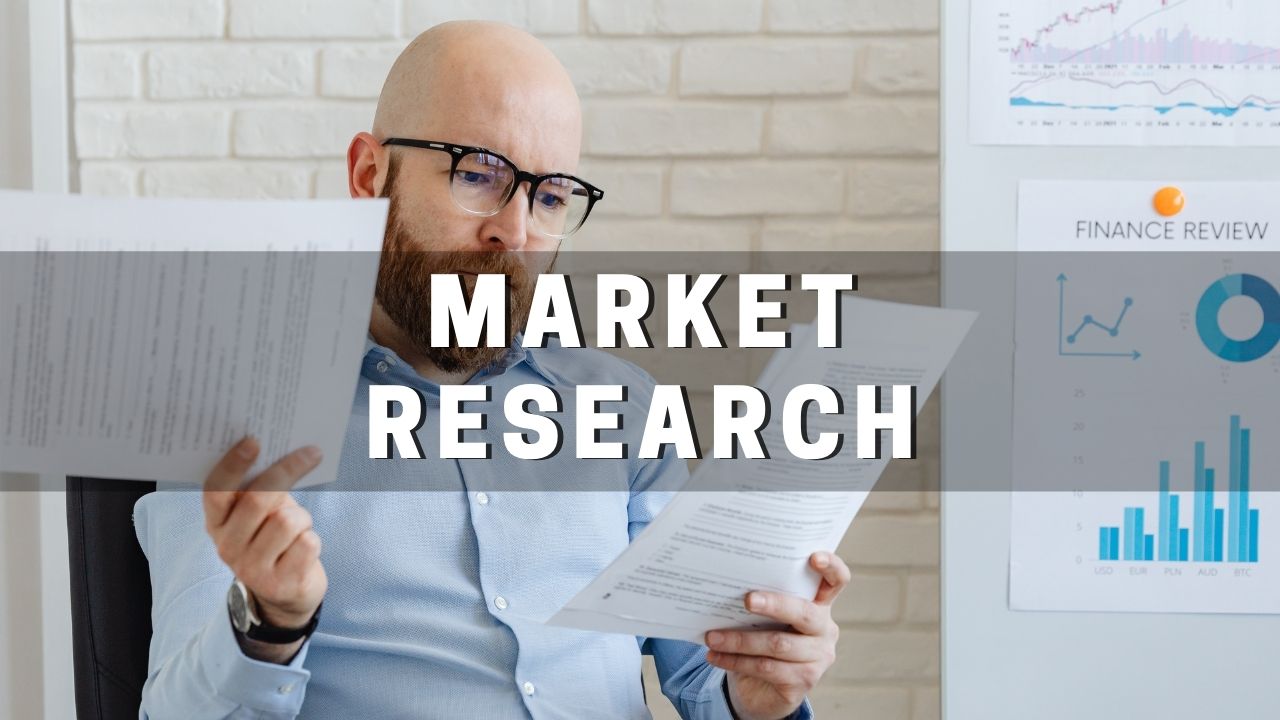
MARKET RESEARCH

PRODUCTIVITY IMPROVEMENT TECHNIQUES AND TOOLS
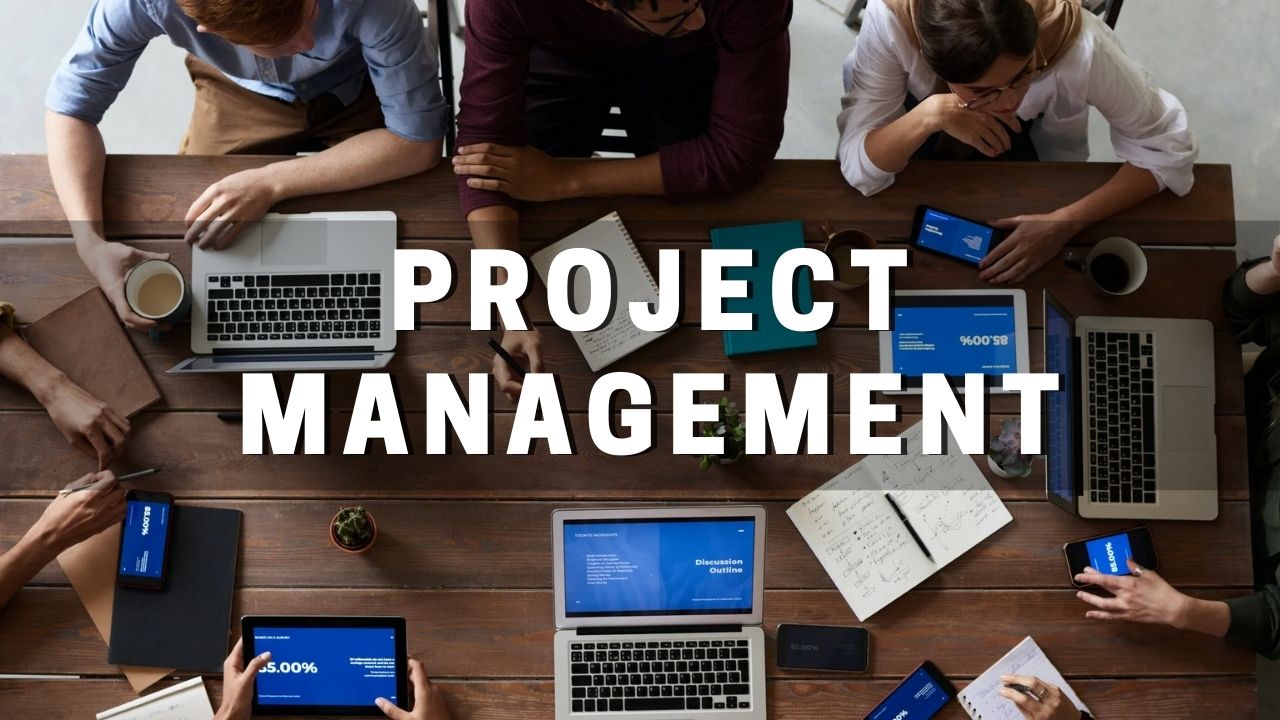
PROJECT MANAGEMENT
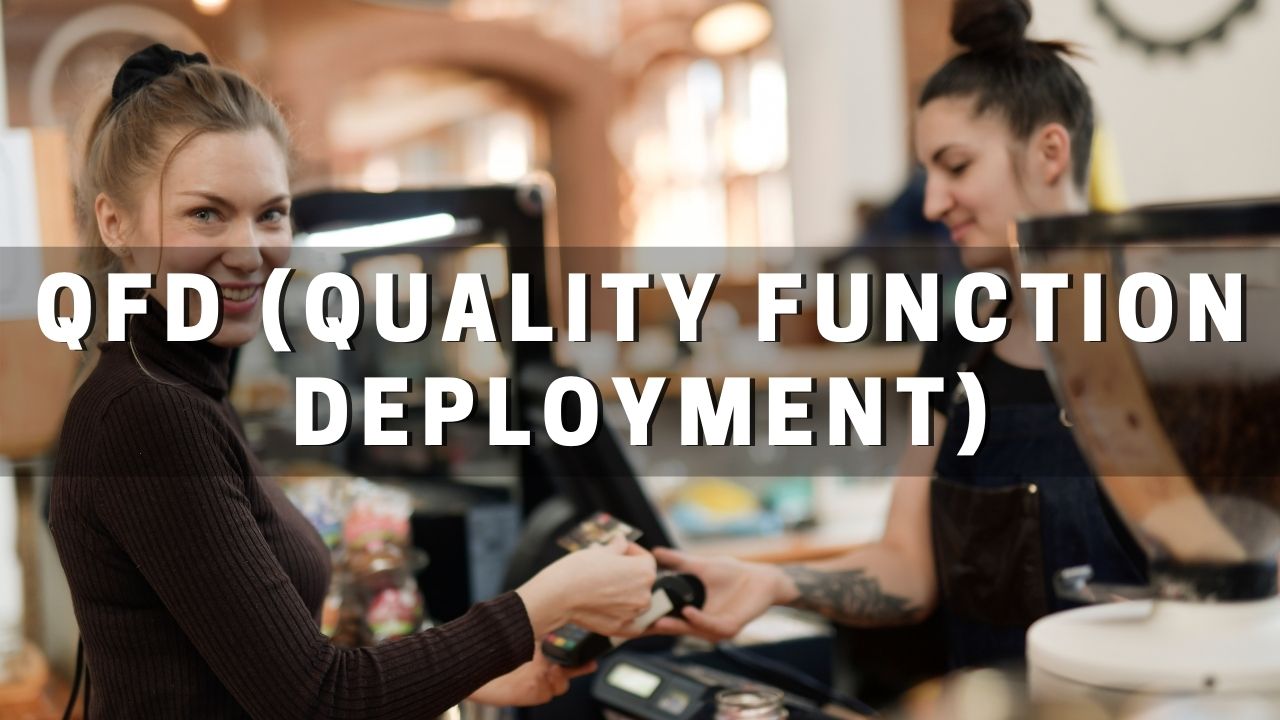
QFD – QUALITY FUNCTION DEPLOYMENT
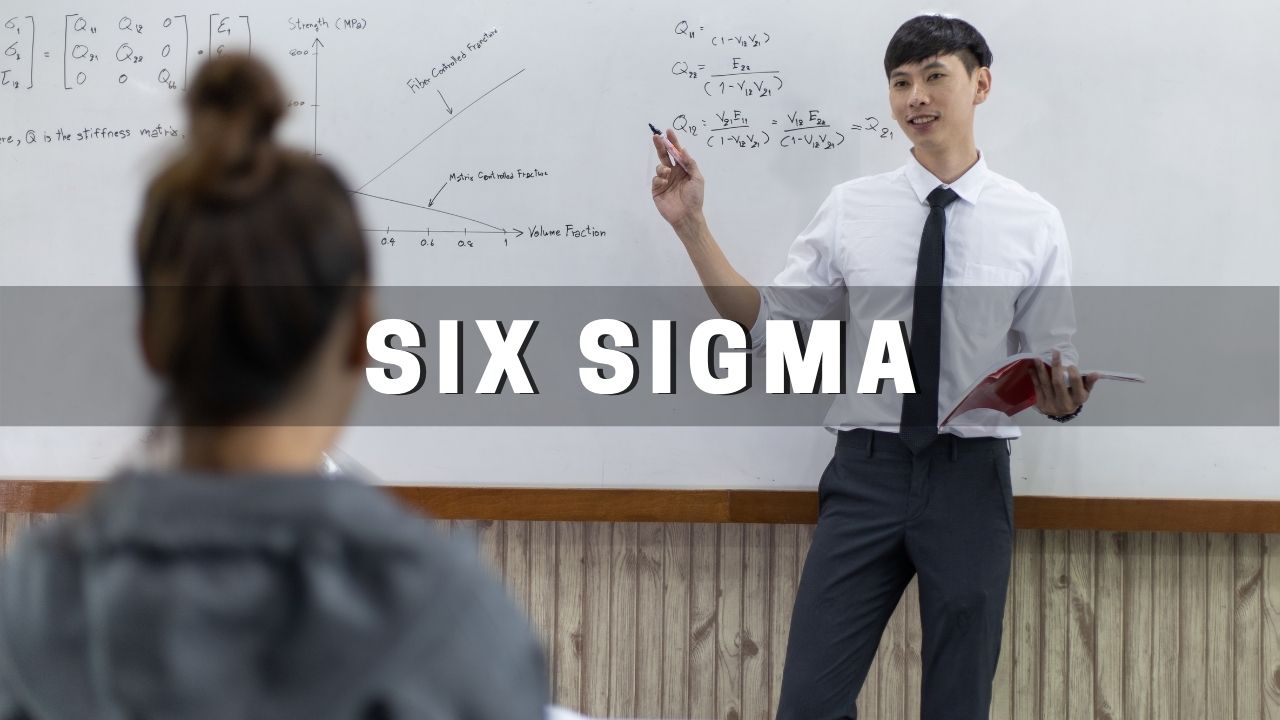
SIX SIGMA
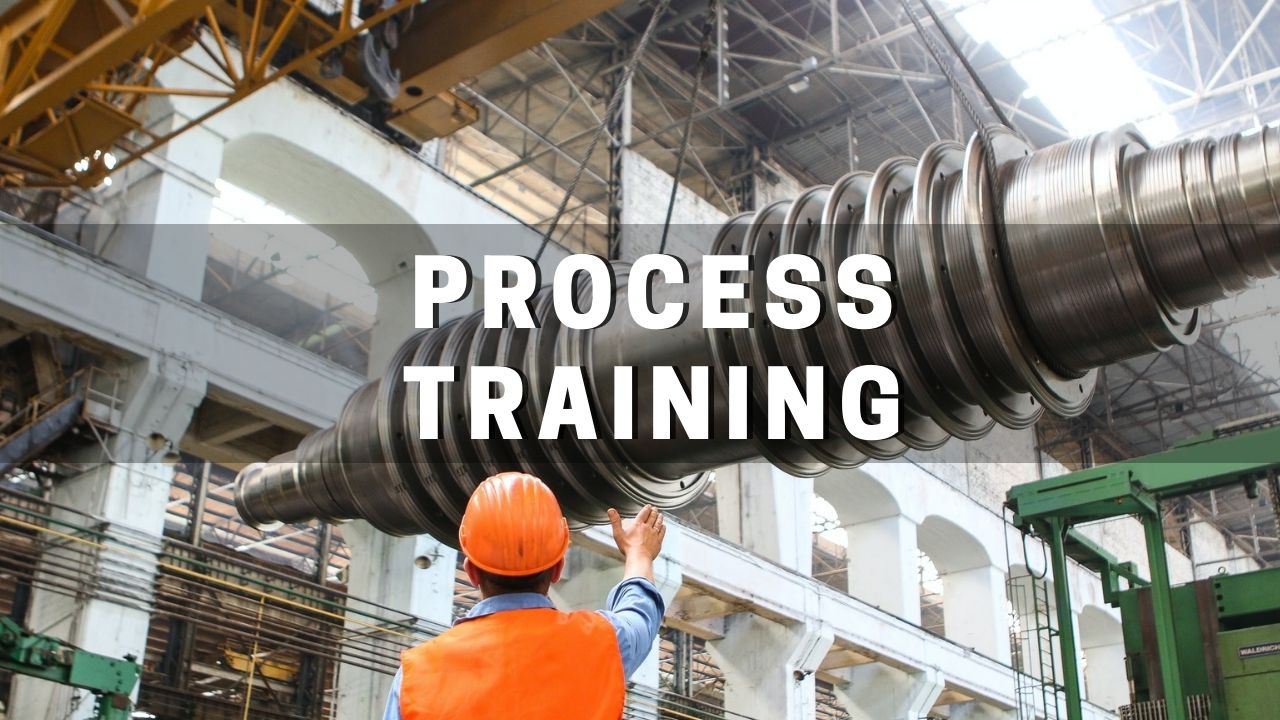
STATISTICAL PROCESS CONTROL
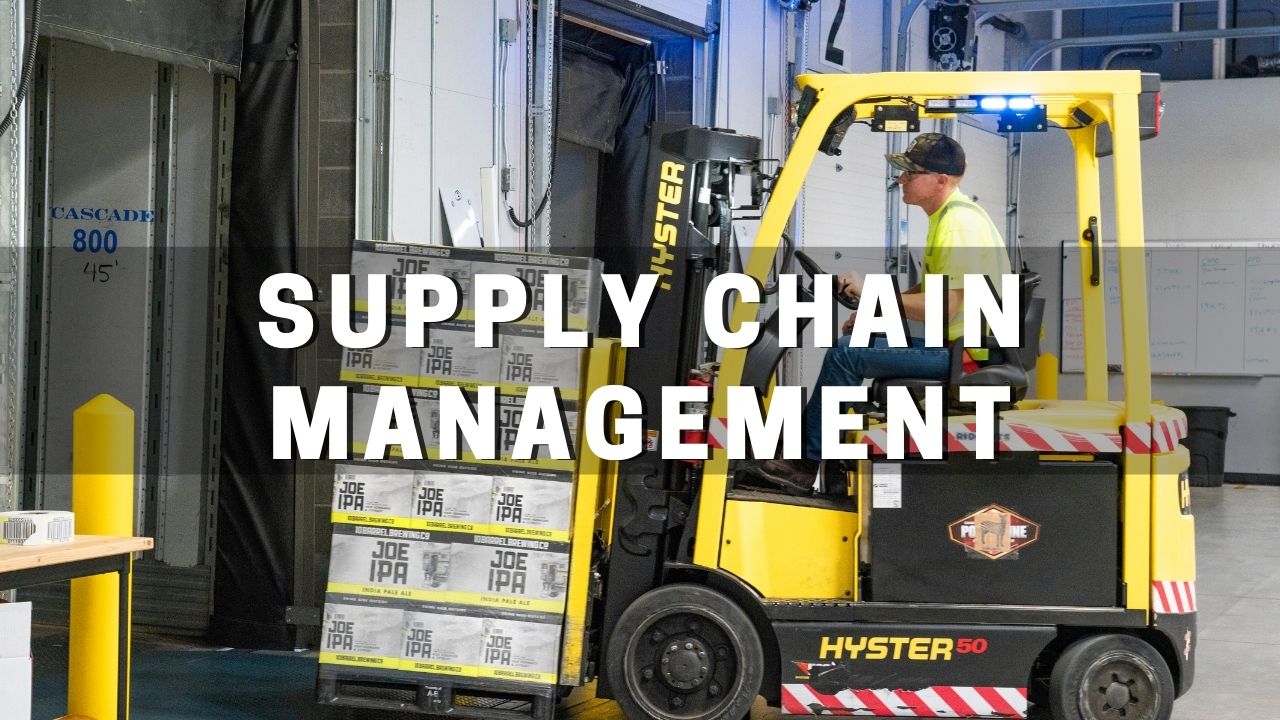
SUPPLY CHAIN MANAGEMENT

TIME MOTION STUDY
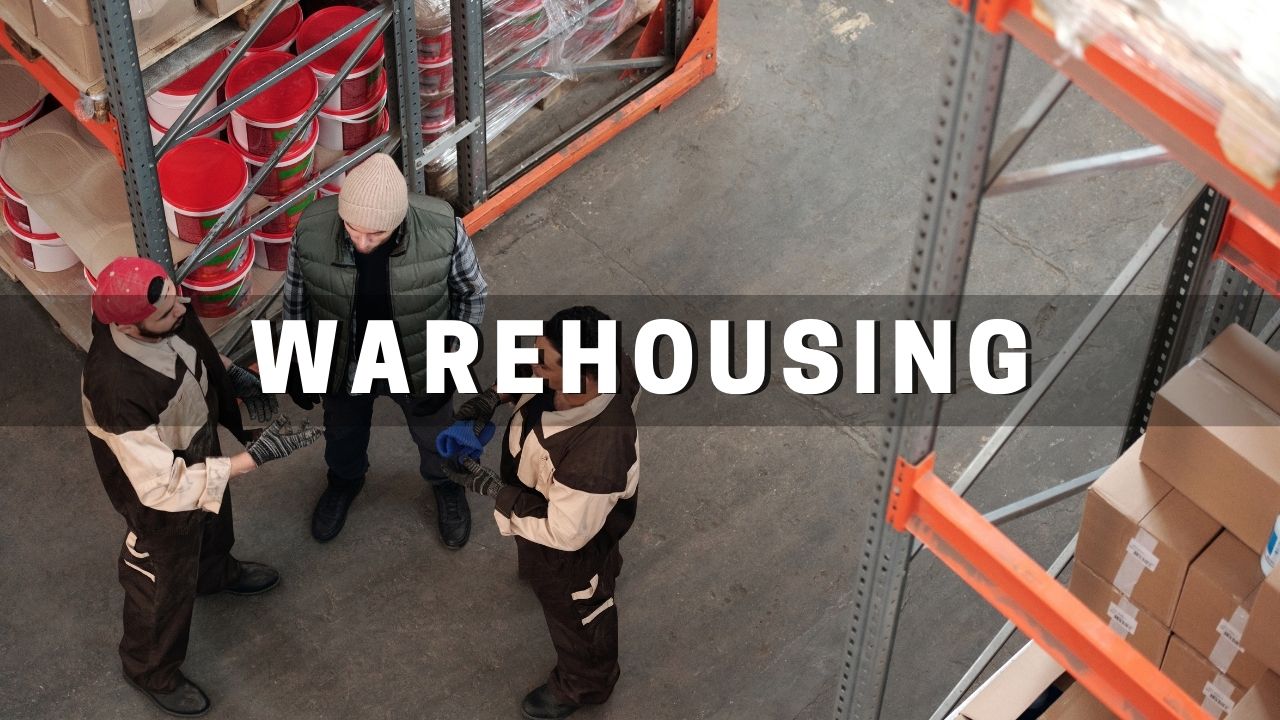
WAREHOUSING & INVENTORY MANAGEMENT
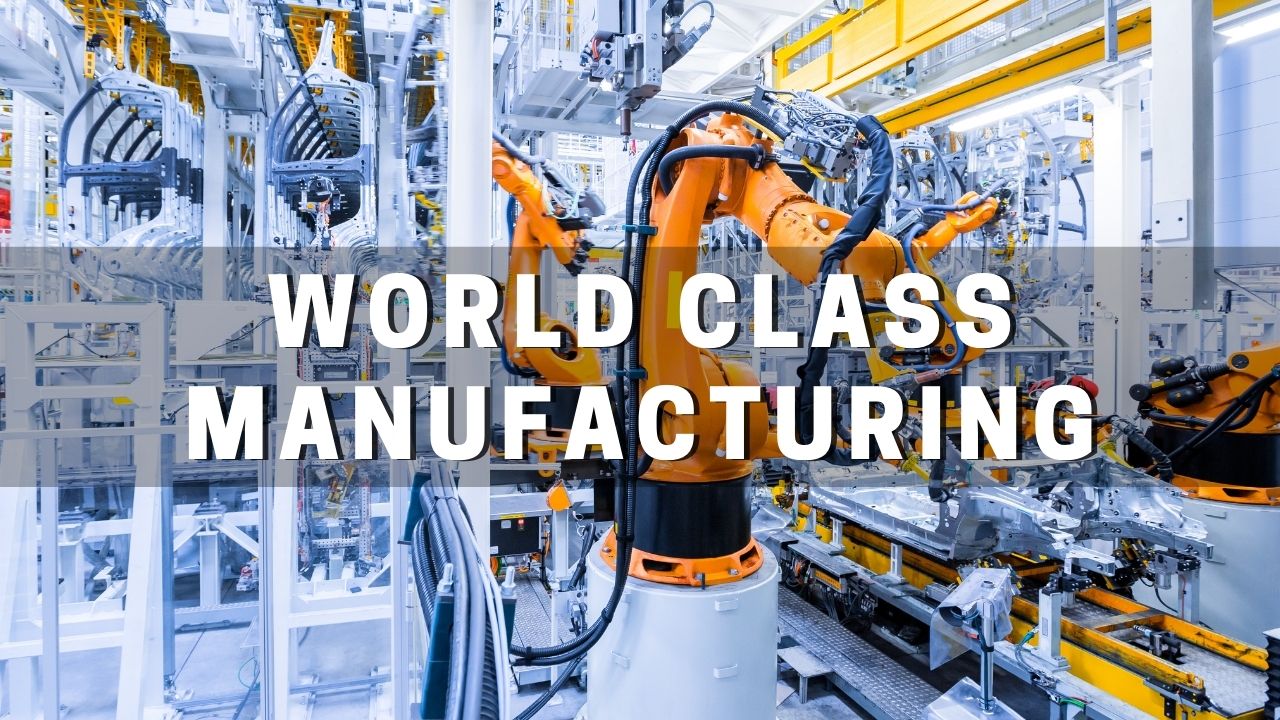
WORLD CLASS MANUFACTURING
Would you like to start a project with us?
Lets work together in a one-of-a-kind, customised training program that combines the power of knowledge, technology and personal coaching.